Пресс центр
Сделано в "Сормово" - треть всех судов "река-море"/Корабел
5 Июня 2018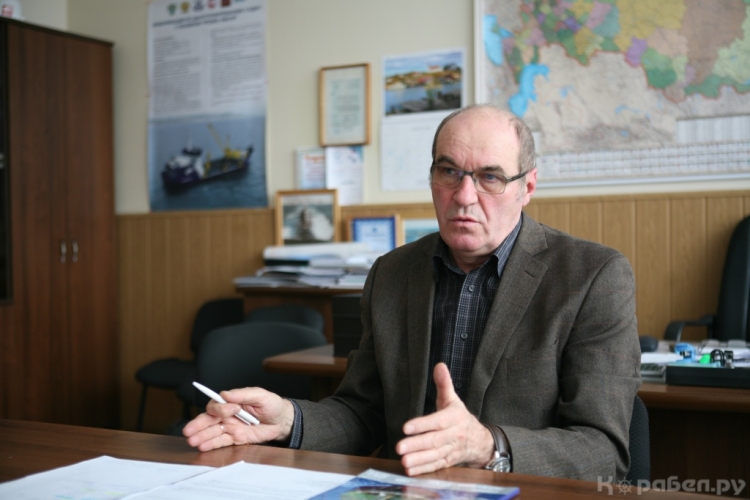
В прошлом номере журнала WWW.KORABEL.RU мы опубликовали аналитический обзор построенных с начала XXI века судах смешанного "река-море" плавания. Напомним, всего за неполных 17 лет судовладельцы получили более 300 единиц новых танкеров и сухогрузов. Третью часть из них передали корабелы завода "Красное Сормово".
О том, как эта масштабная стройка шла на предприятии, нам рассказал директор Инженерного центра Сергей Смирнов. В беседе затронули мы и темы энергосбережения, снижения трудоемкости и другие факторы эффективного коммерческого судостроения.
– "Красное Сормово" – один из немногих отечественных заводов в России, который начиная с нулевых годов занимался строительством обновленных серий судов смешанного плавания. Расскажите немного о том, как это происходило?
– Начиная с конца 90-х, шло интенсивное вымирание старого флота постройки 60-х — 70-х годов XX века. Суда более поздней постройки ("Сормовские" проекта 1557, "Балтийские" проектов 16290 и 16291, некоторые "Волго-Балты") пока работают, но они уже не удовлетворяют требованиям Международных конвенций МАРПОЛ, СОЛАС. Поэтому работают только во внутренних бассейнах страны. Их, конечно, тоже надо менять.
За 16 лет с 2000 по 2016 гг. только завод "Красное Сормово" сдал 107 единиц судов смешанного плавания, а всего за этот период отечественный флот получил 327 судов – цифра немаленькая.
Что касается типов, то сначала был большой спрос на сухогрузы. В период с 1986 по 1998 годы мы сдали большую серию "Волга" проекта 19610 из 45 единиц, а начиная с нулевых пошли заказы на наливной флот.
Поначалу мы работали по проектам Волго-Каспийского ПКБ: построили 5 танкеров проекта 19612, затем 25 единиц пр. 19614, 14 морских танкеров для Каспийского моря – пр. 19619. Потом на рынке начало активно себя позиционировать "Морское инженерное бюро". И сейчас заказчики, как правило, приходят с адаптированным под себя проектом от "МИБ".
По проекту этого КБ мы строим и самую массовую серию танкеров RST27. Всего же с 2012 года мы сдали уже 20 судов и еще на 8 единиц есть контракты.
Но сейчас увеличилась потребность в перевозках генеральных и навалочных грузов в Каспийском регионе со стороны и российских компаний, и казахских, и туркменских. Возрастает активность на шельфе, куда надо доставлять много габаритных грузов, в том числе транзитом из Европы. Поэтому заказчики снова смотрят в сторону сухогрузного флота.
Недавно мы подписали контракт на строительство 5 сухогрузов проекта RSD59, еще по 3-м судам ведем переговоры. Габариты судна и осадка в 4,5 метра позволяют ему проходить все каналы в Единой европейской глубоководной системе. И помимо "Красного Сормова", еще 5 судов этого же проекта будет строить Невский завод.
Также мы надеемся на продолжение развития направления строительства земснарядов. Как вы знаете, в прошлом году мы сдали 3 земснаряда TSHD100 по проекту Damen. Спрос на эти суда в стране большой, а у нас, в свою очередь, есть свои технологические наработки: как улучшить проект, как перейти на отечественное оборудование.
– Вы адаптировали свое производство под строительство новых серий судов?
– "Красное Сормово" в советское время специализировалось на строительстве подводных лодок. Торговые суда на заводе шли как товары народного потребления. С точки зрения оснащения, это хорошо. У нас, например, в цехах установлены 100-тонные краны, и мы можем применять блочный метод строительства. Ту же надстройку мы изготавливаем целиком, потом с помощью двух кранов ставим ее на судно.
Но в то же время военный профиль внес свою каплю дегтя в бочку меда. Лодки более компактные, поэтому для строительства гражданских судов из двух стапелей в каждом пролете эллинга мы можем задействовать только один стапель. Когда переходили на мирные рельсы, мы провели большую подготовку производства. И если раньше собирали отдельные небольшие секции, то сейчас уже работаем с блоками, стараемся использовать максимальные габариты листа. А это уменьшение стыковок, сварки, как следствие – снижение трудоемкости и так далее.
– В свое время суда "МИБ" очень сильно критиковали за большой коэффициент полноты. Они действительно лучше работают по сравнению с "Волгонефтями"?
– Вид у судов "Волго-Дон-макс", на первый взгляд, действительно, непривычный, особенно по сравнению с классическими обводами тех же "Волгонефтей". Но зато они выигрывают в коммерческом плане. За счет большого коэффициента полноты берут на 500 тонн больше груза, нежели классические суда. Это увеличение грузоподъемности почти на 10% при той же осадке и при тех же габаритах.
Глобально и наука, и машиностроение за 25 лет ушли далеко вперед. Сегодняшнее оборудование существенно отличается от того, что было раньше, и по надежности, и по эргономике. Правда, в основном оно импортного производства. Отечественные производители пытаются наверстать технологическое отставание, но несмотря на все программы импортозамещения, ситуация пока тяжелая.
Что будет монтироваться на коммерческом судне, определяет заказчик, и пока он склоняется в сторону зарубежной техники. Но его тоже можно понять. Судно приносит прибыль, только когда ходит, а не стоит в ремонте. Тем более, судовладельцы работают не только в России, а значит, нужно обеспечить весь набор услуг — от сервиса до поставок запасных частей, в том числе за рубеж. А у наших производителей оборудования с этим проблемы.
– За эти годы количество применяемого сортамента металла увеличилось или уменьшилось?
– Раньше работа была более унифицированной. Например, в наружной обшивке судна применялись толщины одного порядка. Сейчас же идет борьба за каждый килограмм перевезенного груза, соответственно конструкторов вынуждают экономить каждый килограмм корпуса.
– Какой прокат вы используете?
– В основном, у нас металл идет из Магнитогорска, но есть и Череповецкий прокат, и прокат с других комбинатов.
– Но у "Северстали" металл идет весь с перекатом...
– Эта проблема уже давно известна. Чтобы найти баланс, мы работали и с конструкторами, и с поставщиками. Только попались на эту удочку, когда строили баржи проекта 82.
Но это была ошибка проектанта, из-за чего корпус баржи вышел на 300 тонн тяжелее. Заказчик понял, в чем причины, претензий к нам не предъявлял, но проблема переката от этого не ушла.
– Давайте вернемся к теплоходам. Насколько снизилась трудоемкость строительства танкера проекта RST27 от головного к серийному и уже к 23-му корпусу?
– В реальной жизни все выходит не так, как написано в учебнике. По многим причинам. Например, начинали мы с чистого танкера, который должен был возить сырую нефть и нефтепродукты. Потом появился вариант химовоза для транспортировки растительного масла. Соответственно поменялся корпус, уже используются другие материалы, поменялась спецификация оборудования. Затем поступил заказ на танкер для перевозки тяжелой химии. Снова проект пришлось переделывать. Поэтому проанализировать изменение трудоемкости достаточно сложно.
Конечно, разница в строительстве головного судна и 23-го есть, но если брать все суда серии целиком, то выясняется, что трудоемкость мало отличается. Поэтому и цена у нас пока не снижается, даже наоборот – увеличивается.
Мы были бы рады строить одинаковые пароходы, но каждый заказчик хочет судно под себя, поэтому мы отталкиваемся от этих пожеланий.
– Как выдерживаете стапельный период?
– Мы стараемся задействовать все имеющиеся стапельные места. В самый насыщенный 2012 год мы сдали 11 единиц танкеров, в этом году по планам сдать 8. В среднем на обработку металла одного корпуса мы закладываем 45 суток, с таким же интервалом планируем сдачу судов Заказчику.
Конечно, некоторую "неразбериху" в работу вносит зимний период, декабрь - февраль в заводской гавани "мертвый сезон". Поэтому первые суда годовой программы мы отправляем в конце апреля – начале мая, а последние в середине ноября.
– Расскажите про серию танкеров разработки Волго-Каспийского ПКБ. На ваш взгляд, их проекты лучше проектов "МИБ"?
– Мы строили несколько серий танкеров по проектам ВК ПКБ – суммарно около 50 единиц. Не могу сказать, какой из них лучше или хуже в эксплуатации, это прерогатива заказчика. Например, проект 19900 очень похож на RST22 разработки "МИБ", но они совершенно разные по начинке. На проекте 19614 была задача сделать "рабочую лошадку". Там двухместные каюты, отдельные санузлы только у комсостава, и автоматизации гораздо меньше, нежели на том же RST27. Есть и более оснащенные проекты.
Но в целом у Волго-Каспийского ПКБ современные, живые суда, соответствующие требованиям дня. Правда, сейчас оно занято, в основном, переносом задумок Геннадия Вячеславовича Егорова на РКД.
– Работа над техпроектами "МИБ" – дело трудозатратное?
– Это, конечно, впечатляет, когда заказчику показывают красивый листок с общим видом танкера или сухогруза. Другое дело, когда приходиться лезть в двойное дно и пытаться сварить конструкцию, до которой уже добраться нельзя.
Но я хочу сказать, что такой труд по реализации идей облагораживает конструкторов, даем им ценный опыт.
– У вас на заводе считают долю энергозатрат в себестоимости продукции?
– Разделить энергозатраты — какие из них ушли в судостроение, какие на спецтехнику — очень трудно. Поэтому мы просто определяем общую долю в масштабах завода.
– А вопросами снижения энергопотребления занимаетесь?
– Конечно! Полностью заменили сварочную технику, поставили полуавтоматы. Навели порядок с системой отопления, полностью отказались от парового отопления. Затем убрали компрессорную станцию, поставили индивидуальные компрессоры в цехах. В районе линии обработки плоских секций у нас уже стоит инфракрасный обогрев, который обеспечивает не только нормальные условия труда человека, но и нужную температуру металла. Такая же система смонтирована и на окрасочном участке.
Здорово урезали металлургическое производство, особенно по сравнению с советским периодом. Но нас к этому подвела сама экономика. Сейчас у нас работают несколько небольших электропечей, но содержим мы их больше для собственных нужд. В производстве спецоборудования есть отдельные металлоизделия, которые не заказать в штучных экземплярах. Надо брать или вагон, или фуру, а нам надо всего 2-3 десятка. Поэтому производим их в наших цехах.
Вообще, мы стараемся следить за последними технологиями удешевления производства.
Источник: Корабел
О том, как эта масштабная стройка шла на предприятии, нам рассказал директор Инженерного центра Сергей Смирнов. В беседе затронули мы и темы энергосбережения, снижения трудоемкости и другие факторы эффективного коммерческого судостроения.
– "Красное Сормово" – один из немногих отечественных заводов в России, который начиная с нулевых годов занимался строительством обновленных серий судов смешанного плавания. Расскажите немного о том, как это происходило?
– Начиная с конца 90-х, шло интенсивное вымирание старого флота постройки 60-х — 70-х годов XX века. Суда более поздней постройки ("Сормовские" проекта 1557, "Балтийские" проектов 16290 и 16291, некоторые "Волго-Балты") пока работают, но они уже не удовлетворяют требованиям Международных конвенций МАРПОЛ, СОЛАС. Поэтому работают только во внутренних бассейнах страны. Их, конечно, тоже надо менять.
За 16 лет с 2000 по 2016 гг. только завод "Красное Сормово" сдал 107 единиц судов смешанного плавания, а всего за этот период отечественный флот получил 327 судов – цифра немаленькая.
Что касается типов, то сначала был большой спрос на сухогрузы. В период с 1986 по 1998 годы мы сдали большую серию "Волга" проекта 19610 из 45 единиц, а начиная с нулевых пошли заказы на наливной флот.
Поначалу мы работали по проектам Волго-Каспийского ПКБ: построили 5 танкеров проекта 19612, затем 25 единиц пр. 19614, 14 морских танкеров для Каспийского моря – пр. 19619. Потом на рынке начало активно себя позиционировать "Морское инженерное бюро". И сейчас заказчики, как правило, приходят с адаптированным под себя проектом от "МИБ".
По проекту этого КБ мы строим и самую массовую серию танкеров RST27. Всего же с 2012 года мы сдали уже 20 судов и еще на 8 единиц есть контракты.
Но сейчас увеличилась потребность в перевозках генеральных и навалочных грузов в Каспийском регионе со стороны и российских компаний, и казахских, и туркменских. Возрастает активность на шельфе, куда надо доставлять много габаритных грузов, в том числе транзитом из Европы. Поэтому заказчики снова смотрят в сторону сухогрузного флота.
Недавно мы подписали контракт на строительство 5 сухогрузов проекта RSD59, еще по 3-м судам ведем переговоры. Габариты судна и осадка в 4,5 метра позволяют ему проходить все каналы в Единой европейской глубоководной системе. И помимо "Красного Сормова", еще 5 судов этого же проекта будет строить Невский завод.
Также мы надеемся на продолжение развития направления строительства земснарядов. Как вы знаете, в прошлом году мы сдали 3 земснаряда TSHD100 по проекту Damen. Спрос на эти суда в стране большой, а у нас, в свою очередь, есть свои технологические наработки: как улучшить проект, как перейти на отечественное оборудование.
– Вы адаптировали свое производство под строительство новых серий судов?
– "Красное Сормово" в советское время специализировалось на строительстве подводных лодок. Торговые суда на заводе шли как товары народного потребления. С точки зрения оснащения, это хорошо. У нас, например, в цехах установлены 100-тонные краны, и мы можем применять блочный метод строительства. Ту же надстройку мы изготавливаем целиком, потом с помощью двух кранов ставим ее на судно.
Но в то же время военный профиль внес свою каплю дегтя в бочку меда. Лодки более компактные, поэтому для строительства гражданских судов из двух стапелей в каждом пролете эллинга мы можем задействовать только один стапель. Когда переходили на мирные рельсы, мы провели большую подготовку производства. И если раньше собирали отдельные небольшие секции, то сейчас уже работаем с блоками, стараемся использовать максимальные габариты листа. А это уменьшение стыковок, сварки, как следствие – снижение трудоемкости и так далее.
– В свое время суда "МИБ" очень сильно критиковали за большой коэффициент полноты. Они действительно лучше работают по сравнению с "Волгонефтями"?
– Вид у судов "Волго-Дон-макс", на первый взгляд, действительно, непривычный, особенно по сравнению с классическими обводами тех же "Волгонефтей". Но зато они выигрывают в коммерческом плане. За счет большого коэффициента полноты берут на 500 тонн больше груза, нежели классические суда. Это увеличение грузоподъемности почти на 10% при той же осадке и при тех же габаритах.
Глобально и наука, и машиностроение за 25 лет ушли далеко вперед. Сегодняшнее оборудование существенно отличается от того, что было раньше, и по надежности, и по эргономике. Правда, в основном оно импортного производства. Отечественные производители пытаются наверстать технологическое отставание, но несмотря на все программы импортозамещения, ситуация пока тяжелая.
Что будет монтироваться на коммерческом судне, определяет заказчик, и пока он склоняется в сторону зарубежной техники. Но его тоже можно понять. Судно приносит прибыль, только когда ходит, а не стоит в ремонте. Тем более, судовладельцы работают не только в России, а значит, нужно обеспечить весь набор услуг — от сервиса до поставок запасных частей, в том числе за рубеж. А у наших производителей оборудования с этим проблемы.
– За эти годы количество применяемого сортамента металла увеличилось или уменьшилось?
– Раньше работа была более унифицированной. Например, в наружной обшивке судна применялись толщины одного порядка. Сейчас же идет борьба за каждый килограмм перевезенного груза, соответственно конструкторов вынуждают экономить каждый килограмм корпуса.
– Какой прокат вы используете?
– В основном, у нас металл идет из Магнитогорска, но есть и Череповецкий прокат, и прокат с других комбинатов.
– Но у "Северстали" металл идет весь с перекатом...
– Эта проблема уже давно известна. Чтобы найти баланс, мы работали и с конструкторами, и с поставщиками. Только попались на эту удочку, когда строили баржи проекта 82.
Но это была ошибка проектанта, из-за чего корпус баржи вышел на 300 тонн тяжелее. Заказчик понял, в чем причины, претензий к нам не предъявлял, но проблема переката от этого не ушла.
– Давайте вернемся к теплоходам. Насколько снизилась трудоемкость строительства танкера проекта RST27 от головного к серийному и уже к 23-му корпусу?
– В реальной жизни все выходит не так, как написано в учебнике. По многим причинам. Например, начинали мы с чистого танкера, который должен был возить сырую нефть и нефтепродукты. Потом появился вариант химовоза для транспортировки растительного масла. Соответственно поменялся корпус, уже используются другие материалы, поменялась спецификация оборудования. Затем поступил заказ на танкер для перевозки тяжелой химии. Снова проект пришлось переделывать. Поэтому проанализировать изменение трудоемкости достаточно сложно.
Конечно, разница в строительстве головного судна и 23-го есть, но если брать все суда серии целиком, то выясняется, что трудоемкость мало отличается. Поэтому и цена у нас пока не снижается, даже наоборот – увеличивается.
Мы были бы рады строить одинаковые пароходы, но каждый заказчик хочет судно под себя, поэтому мы отталкиваемся от этих пожеланий.
– Как выдерживаете стапельный период?
– Мы стараемся задействовать все имеющиеся стапельные места. В самый насыщенный 2012 год мы сдали 11 единиц танкеров, в этом году по планам сдать 8. В среднем на обработку металла одного корпуса мы закладываем 45 суток, с таким же интервалом планируем сдачу судов Заказчику.
Конечно, некоторую "неразбериху" в работу вносит зимний период, декабрь - февраль в заводской гавани "мертвый сезон". Поэтому первые суда годовой программы мы отправляем в конце апреля – начале мая, а последние в середине ноября.
– Расскажите про серию танкеров разработки Волго-Каспийского ПКБ. На ваш взгляд, их проекты лучше проектов "МИБ"?
– Мы строили несколько серий танкеров по проектам ВК ПКБ – суммарно около 50 единиц. Не могу сказать, какой из них лучше или хуже в эксплуатации, это прерогатива заказчика. Например, проект 19900 очень похож на RST22 разработки "МИБ", но они совершенно разные по начинке. На проекте 19614 была задача сделать "рабочую лошадку". Там двухместные каюты, отдельные санузлы только у комсостава, и автоматизации гораздо меньше, нежели на том же RST27. Есть и более оснащенные проекты.
Но в целом у Волго-Каспийского ПКБ современные, живые суда, соответствующие требованиям дня. Правда, сейчас оно занято, в основном, переносом задумок Геннадия Вячеславовича Егорова на РКД.
– Работа над техпроектами "МИБ" – дело трудозатратное?
– Это, конечно, впечатляет, когда заказчику показывают красивый листок с общим видом танкера или сухогруза. Другое дело, когда приходиться лезть в двойное дно и пытаться сварить конструкцию, до которой уже добраться нельзя.
Но я хочу сказать, что такой труд по реализации идей облагораживает конструкторов, даем им ценный опыт.
– У вас на заводе считают долю энергозатрат в себестоимости продукции?
– Разделить энергозатраты — какие из них ушли в судостроение, какие на спецтехнику — очень трудно. Поэтому мы просто определяем общую долю в масштабах завода.
– А вопросами снижения энергопотребления занимаетесь?
– Конечно! Полностью заменили сварочную технику, поставили полуавтоматы. Навели порядок с системой отопления, полностью отказались от парового отопления. Затем убрали компрессорную станцию, поставили индивидуальные компрессоры в цехах. В районе линии обработки плоских секций у нас уже стоит инфракрасный обогрев, который обеспечивает не только нормальные условия труда человека, но и нужную температуру металла. Такая же система смонтирована и на окрасочном участке.
Здорово урезали металлургическое производство, особенно по сравнению с советским периодом. Но нас к этому подвела сама экономика. Сейчас у нас работают несколько небольших электропечей, но содержим мы их больше для собственных нужд. В производстве спецоборудования есть отдельные металлоизделия, которые не заказать в штучных экземплярах. Надо брать или вагон, или фуру, а нам надо всего 2-3 десятка. Поэтому производим их в наших цехах.
Вообще, мы стараемся следить за последними технологиями удешевления производства.
Источник: Корабел
Мы в Facebook
Возврат к списку